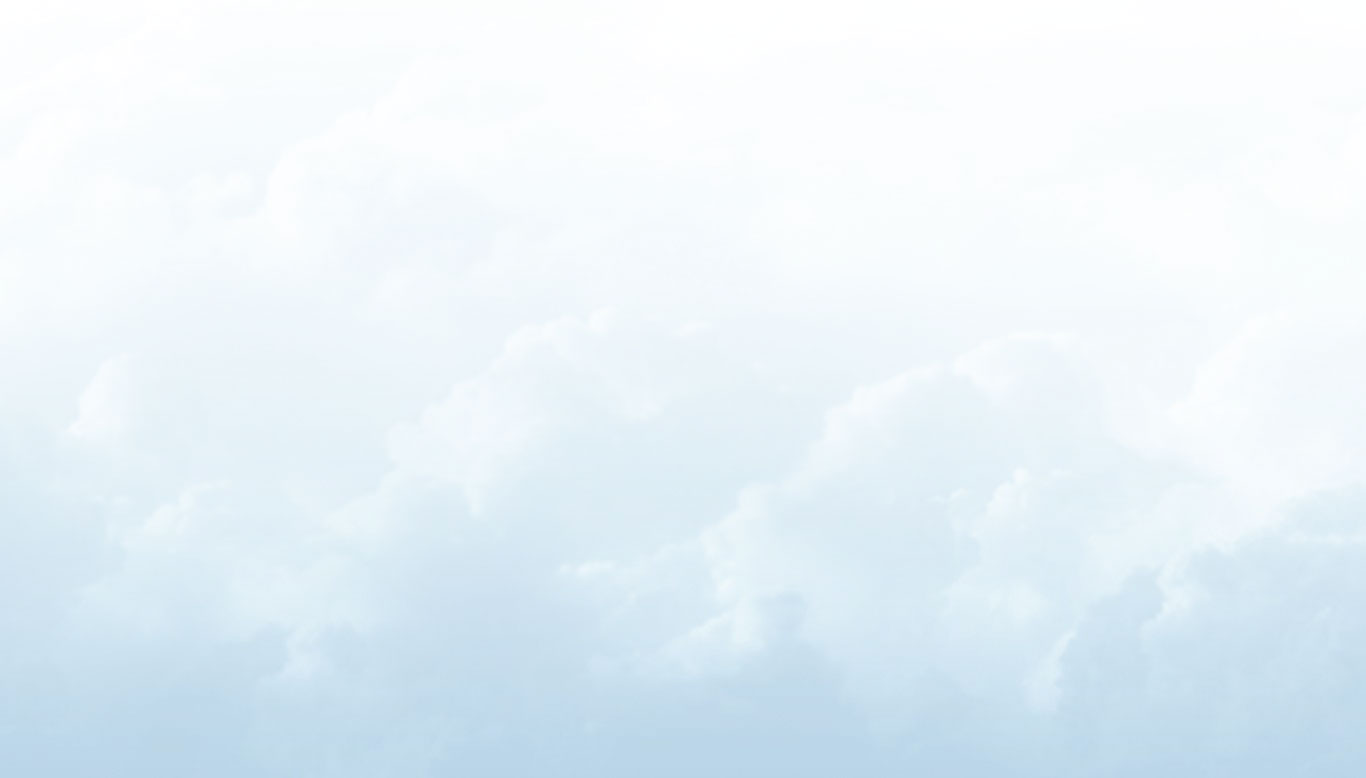

Quality service management
Senior management of the Company emphasizes the importance of quality service management within the organization. They collaborate to carefully consider and establish a Quality Policy that is aligned with the organization's purpose, context, and strategies in the aviation industry, as well as complied with relevant laws and standards pertaining to the aviation business. This Quality Policy serves as a framework for defining the Company's Quality Objectives at the organizational level. These objectives serve as targets for controlling the quality of service delivery according to the Company's quality management system.
The Quality Policy of the Company is documented as a quality document and requires approval from the highest-level executives. It also includes a system for controlling quality documents as per the requirements of the quality management system, as well as a communication system to ensure employees throughout the Company are aware of and understand the policy. Additionally, it is ready for dissemination of information to stakeholders.
Furthermore, the Company's Quality Policy undergoes periodic review and evaluation by senior management at least twice a year. This is done to continuously improve and develop work processes and the quality management system in service delivery, following the requirements of the applied quality management system within the Company.
Quality control process to meet established standards:
- Quality Documents:
- The Quality Procedure (QP) document covers all work processes and ensures the creation of related documents such as Work Instructions (WI), Forms (FM), Supporting Documents (SD), and List of Records (LR) that are aligned with the QP. This ensures completeness, comprehensiveness, and usefulness of the documents as references for employees and relevant individuals.
- In every work process defined by the QP, Key Performance Indicators (KPIs) are established as measurable targets to assess the effectiveness of the work performed in each process.
- In every work process defined by the QP, Key Risk and Opportunity Identification (KRI) documents are created to evaluate risks associated with each process and identify potential opportunities.
- Requirements and expectations of interested parties (IN) are documented at every organizational level based on the organizational chart.
These quality documents adhere to established principles and methods for developing the Company's quality documents, ensuring clarity and standardization. The Company also implements its own Document Control System (PGE-ISO) to facilitate quick and convenient access to and understanding of various work documents, in line with ISO 9001:2015 requirements and other applicable standards endorsed and applied by the Company.
- Internal Audit
- Internal audits within the Company cover all dimensions related to the Company's airline business, including safety standards, quality management systems, internal control, and information systems.
- External Audit
- External audits involve the assessment of safety standards and quality management systems.
The certification body (CB) that evaluates and certifies the Company's ISO 9001:2015 Quality Management System is United Registrar of Systems (Thailand) Ltd., known as United Registrar of Systems (URS). URS is accredited by UKAS (United Kingdom Accreditation Service) and IATF (International Automotive Task Force). URS has also been appointed as a certified food business establishment by the Food and Drug Administration (FDA). URS conducts regular audits of the Company according to the defined audit cycle:
- Surveillance visits, conducted twice a year to monitor the maintenance of the ISO 9001:2015 Quality Management System.
- Re-certification audits, conducted every three years to renew the ISO 9001:2015 certification.
Despite the impact of the COVID-19 situation, URS, as the certification body, has been able to perform document reviews and on-site audits of operational practices at various units and stations according to the planned schedule. The surveillance visit conducted by URS in 2022 did not identify any non-compliance issues (NC) or major breakdowns that would affect the Company's quality management system. This allows the Company to maintain its ISO 9001:2015 certification.